日期:2017-02-09 / 人气: / 来源:www.biglss.com / 热门标签: 凯发k8官网下载客户端首页 凯发k8官网下载客户端首页
制造系统现状
通过对制造现场初步了解情况,博革咨询团队看到目前制造系统中各方面需要改善的地方,主要从以下几个方面进行阐述:
-员工环境及参与:
1、公司是国营企业体制,员工稳定性较好,目前员工流失率不到每年10%,但是对于工厂持续稳定的制造质量、生产效率等绩效仍然带来很大挑战;员工普遍比较年轻,对我们的人力资源政策有很大挑战;
2、员工采用个人计件工资报酬制,对于生产管理现代化成为很大阻碍;
3、目前的公司范围内的持续改善工作限于高层以及中层有限范围内的项目改善;合理化建议制度流于形式,没有真正起到作用;
4、员工层次参与持续改善的机会和要求不多,全员的持续改善开展不够;没有自发的员工团队参与改善行动。
5、由于公司收益表现较好,员工持续改善的压力不够。各部门分解的kpi要求达不到先进管理要求,离精益生产要求甚远;没有对制造系统的有效跟进、优化提供足够的数据支持;
6、没有有效的“合理化建议”制度,没有系统的使全体员工纳入持续改善的计划和实施行动。
7、经常有各种先进管理思想以及工具培训给予管理人员,但是给予全体员工的培训和解决问题工具、方法不够。
-现场管理:
现场5s情况做的不好。工厂是新厂房,清洁程度较好,但是“三定”标示情况较低;应用目视化管理工具很少;在生产现场管理水平还比较粗放,没有对生产情况进行有效受控,有较大改善余地:
1.车间地面清洁程度较好,有部分地面线区域线的划分,但是没有统一规划物品放置的要求以及地面线标准;5s基本还没有全面有效开展;车间部分生产区域照明不足;现场原物料、在制品等堆放较随意,没有很有效的管理和分类以及降低库存的措施;存在物料标识不明状态不清现象;成品摆放较随意;因为生产区域占用面积大,没有成品库存区域,所以成品露天摆放在厂区内其他地方;
2.没有有效的现场生产每小时的生产状况数据记录、质量数据、设备状况等信息,不利于管理人员有效监控现场的生产、品质状况;
3.生产流程并不复杂,分2个车间:“自制装置”和“装配”,但是生产中存在大量浪费现象:过量生产、库存、等待、返工、不增值过程和动作、搬运等;员工对于消除浪费意识和行动非常缺乏,现场的各种浪费都存在而且没有得到重视和引导消除浪费。
4.生产组织中沿用传统的大规模批量生产方式,并且生产批量没有确定标准,实行按单生产;工序间的物料停滞等待顿现象比较严重,缺乏整体“物料流动”的概念,现场在制品较多;“孤岛”式生产;库存必然掩盖问题,使得整体状况得不到改善;
5.生产现场对异常状况反映没有很明显的信号,从而不容易使大家关注;没有生产时间损失记录等;
-品质系统:
1.有实施必要的品质保证体系(iso9000)以及必要的品质计划;质量问题在整个工厂里有传达交流迹象,但是提高质量的重要性仍在生产需要之下;
2.品质问题基本是事后检查,没有迹象表现良好的预防性品质改善;一线员工以及管理人员更重视发现缺陷,相关的改善活动比较欠缺。
3.大多数质检是按计划,在线/在工位上进行的。工序的一次合格率不高,没有应用衡量制程能力来改善的迹象,工序的稳定性也未得到有效检测;
4.注意到提高质量和生产力的机会并制订了一些计划方案。但只有有限的跨功能部门支持力量;对关键员工进行了解决问题方法的训练,但是并没有被更广泛地贯彻使用。
-运作效率:
1.装配区的设置没有按照流程工艺安排布局,大屏在总装场地上安装不会移动,等待时间长,隐性的生产能力损失严重,生产效率低下,同时生产质量得不到充分保证;
2.生产工序工艺流程不合理导致生产安排中效率损失严重,没有细分每个工序要求,必然不能有效控制每个工序节拍时间,进而进行改善,不断提高生产效率;
3.生产中没有大量的设备,也比较缺少设备综合运行效率(oee)的概念。损失时间和停机时间没有区别。
4.对于有限的设备以及共装夹具的使用保养管理不是很规范;设备维护是集团统一,需要公司外部资源,导致一旦有维修保养需求,需要时间等待。
5.自制装置车间内生产流程也是属于“孤岛”式大批量生产方式,内部生产流程不通畅,生产效率低下,并且看不到改善方向;
6.因为生产批量大,换型压力小,但是代价就是生产周期长,库存大;
-物料流动:
1、客户要求的lt交货周期时间平均约为45天,目前的准时交货率约为50%左右,相当的订单并不能够满足客户需求;
2、物料的收货和出货没有按照jit—准时化的要求进行,对供应商的要求还没有达到这种高度;
3、供应商的供货状况有被追踪调查或报告,但是因为约90%为省外供应商,采购周期较长,部分海外采购原物料交货周期甚至达到45天时间,给原物料库存带来很大压力;一次成套率70%左右;
4、总库存周转次数约为5次,从制造流程情况来看,有较多改善潜力存在;(因为没有库存进一步的数据参考,没法具体到每部分库存的分析)
5、装配车间内在制品库存542件大屏,约相当于1.4个月客户需求,制造周期长;
6、自制装置车间孤岛式生产流程导致生产周期长,再加上生产计划问题,不能有效满足后工序生产问题;
7、自制装置车间与装配车间之间存在大量库存,约相当于半个月客户需求;
8、生产组织方式属于典型的大批量推动式生产,但是客户需求是要求特殊定制产品,小批量要求,交货周期要求越来越短;
9、厂内物料是以非标准包装数量的形式储存的(或者没有很好的标准化),更加没有减小物料流通包装数量的行动(标准化、小批量是精益生产永远的要求!);由于制造流程的流动性不够,在制品库存有较大改善余地。
10、厂内物流还没有看到任何使用“拉动式物流”的迹象。各车间之间的物流分割导致制造的流动性差,影响制造周期缩短;
-流动化制造:
1、没有价值流的概念,虽然使用了产品族分类并且按照产品族制定制造组织架构,但是缺乏流动的概念,没有按照产品族价值流跟进改善整个流程
2、没有应用“制造周期mct”来衡量目前的制造现状以及改善幅度;
3、公司按照订单生产,按照订单发货;整个订单处理过程有些复杂,对技术处理环节会有较高要求,目前技术处理周期约为2~10天;
4、生产批量没有标准,按照生产订单数量投入生产,没有持续不断减低生产批量的概念。
5、物料大批量地在工位间流动。但是整体流程方面缺乏流动的概念,导致了过度生产;对在制品库存的储存场地组织仍然是推动式的生产方式。
从整体情况看,现场管理体系还不够精细化,没有有效的持续改善体系在起作用,没有全员的持续改善的观念和系统支持。生产运作效率体系方面做的不够。人员状态不够积极,没有迹象显示充分参与生产管理与改善。整个制造体系还有很多改善的余地。
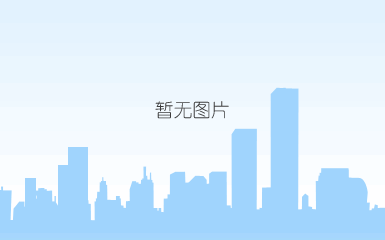
通过对制造现场初步了解情况,博革咨询团队看到目前制造系统中各方面需要改善的地方,主要从以下几个方面进行阐述:
-员工环境及参与:
1、公司是国营企业体制,员工稳定性较好,目前员工流失率不到每年10%,但是对于工厂持续稳定的制造质量、生产效率等绩效仍然带来很大挑战;员工普遍比较年轻,对我们的人力资源政策有很大挑战;
2、员工采用个人计件工资报酬制,对于生产管理现代化成为很大阻碍;
3、目前的公司范围内的持续改善工作限于高层以及中层有限范围内的项目改善;合理化建议制度流于形式,没有真正起到作用;
4、员工层次参与持续改善的机会和要求不多,全员的持续改善开展不够;没有自发的员工团队参与改善行动。
5、由于公司收益表现较好,员工持续改善的压力不够。各部门分解的kpi要求达不到先进管理要求,离精益生产要求甚远;没有对制造系统的有效跟进、优化提供足够的数据支持;
6、没有有效的“合理化建议”制度,没有系统的使全体员工纳入持续改善的计划和实施行动。
7、经常有各种先进管理思想以及工具培训给予管理人员,但是给予全体员工的培训和解决问题工具、方法不够。
-现场管理:
现场5s情况做的不好。工厂是新厂房,清洁程度较好,但是“三定”标示情况较低;应用目视化管理工具很少;在生产现场管理水平还比较粗放,没有对生产情况进行有效受控,有较大改善余地:
1.车间地面清洁程度较好,有部分地面线区域线的划分,但是没有统一规划物品放置的要求以及地面线标准;5s基本还没有全面有效开展;车间部分生产区域照明不足;现场原物料、在制品等堆放较随意,没有很有效的管理和分类以及降低库存的措施;存在物料标识不明状态不清现象;成品摆放较随意;因为生产区域占用面积大,没有成品库存区域,所以成品露天摆放在厂区内其他地方;
2.没有有效的现场生产每小时的生产状况数据记录、质量数据、设备状况等信息,不利于管理人员有效监控现场的生产、品质状况;
3.生产流程并不复杂,分2个车间:“自制装置”和“装配”,但是生产中存在大量浪费现象:过量生产、库存、等待、返工、不增值过程和动作、搬运等;员工对于消除浪费意识和行动非常缺乏,现场的各种浪费都存在而且没有得到重视和引导消除浪费。
4.生产组织中沿用传统的大规模批量生产方式,并且生产批量没有确定标准,实行按单生产;工序间的物料停滞等待顿现象比较严重,缺乏整体“物料流动”的概念,现场在制品较多;“孤岛”式生产;库存必然掩盖问题,使得整体状况得不到改善;
5.生产现场对异常状况反映没有很明显的信号,从而不容易使大家关注;没有生产时间损失记录等;
-品质系统:
1.有实施必要的品质保证体系(iso9000)以及必要的品质计划;质量问题在整个工厂里有传达交流迹象,但是提高质量的重要性仍在生产需要之下;
2.品质问题基本是事后检查,没有迹象表现良好的预防性品质改善;一线员工以及管理人员更重视发现缺陷,相关的改善活动比较欠缺。
3.大多数质检是按计划,在线/在工位上进行的。工序的一次合格率不高,没有应用衡量制程能力来改善的迹象,工序的稳定性也未得到有效检测;
4.注意到提高质量和生产力的机会并制订了一些计划方案。但只有有限的跨功能部门支持力量;对关键员工进行了解决问题方法的训练,但是并没有被更广泛地贯彻使用。
-运作效率:
1.装配区的设置没有按照流程工艺安排布局,大屏在总装场地上安装不会移动,等待时间长,隐性的生产能力损失严重,生产效率低下,同时生产质量得不到充分保证;
2.生产工序工艺流程不合理导致生产安排中效率损失严重,没有细分每个工序要求,必然不能有效控制每个工序节拍时间,进而进行改善,不断提高生产效率;
3.生产中没有大量的设备,也比较缺少设备综合运行效率(oee)的概念。损失时间和停机时间没有区别。
4.对于有限的设备以及共装夹具的使用保养管理不是很规范;设备维护是集团统一,需要公司外部资源,导致一旦有维修保养需求,需要时间等待。
5.自制装置车间内生产流程也是属于“孤岛”式大批量生产方式,内部生产流程不通畅,生产效率低下,并且看不到改善方向;
6.因为生产批量大,换型压力小,但是代价就是生产周期长,库存大;
-物料流动:
1、客户要求的lt交货周期时间平均约为45天,目前的准时交货率约为50%左右,相当的订单并不能够满足客户需求;
2、物料的收货和出货没有按照jit—准时化的要求进行,对供应商的要求还没有达到这种高度;
3、供应商的供货状况有被追踪调查或报告,但是因为约90%为省外供应商,采购周期较长,部分海外采购原物料交货周期甚至达到45天时间,给原物料库存带来很大压力;一次成套率70%左右;
4、总库存周转次数约为5次,从制造流程情况来看,有较多改善潜力存在;(因为没有库存进一步的数据参考,没法具体到每部分库存的分析)
5、装配车间内在制品库存542件大屏,约相当于1.4个月客户需求,制造周期长;
6、自制装置车间孤岛式生产流程导致生产周期长,再加上生产计划问题,不能有效满足后工序生产问题;
7、自制装置车间与装配车间之间存在大量库存,约相当于半个月客户需求;
8、生产组织方式属于典型的大批量推动式生产,但是客户需求是要求特殊定制产品,小批量要求,交货周期要求越来越短;
9、厂内物料是以非标准包装数量的形式储存的(或者没有很好的标准化),更加没有减小物料流通包装数量的行动(标准化、小批量是精益生产永远的要求!);由于制造流程的流动性不够,在制品库存有较大改善余地。
10、厂内物流还没有看到任何使用“拉动式物流”的迹象。各车间之间的物流分割导致制造的流动性差,影响制造周期缩短;
-流动化制造:
1、没有价值流的概念,虽然使用了产品族分类并且按照产品族制定制造组织架构,但是缺乏流动的概念,没有按照产品族价值流跟进改善整个流程
2、没有应用“制造周期mct”来衡量目前的制造现状以及改善幅度;
3、公司按照订单生产,按照订单发货;整个订单处理过程有些复杂,对技术处理环节会有较高要求,目前技术处理周期约为2~10天;
4、生产批量没有标准,按照生产订单数量投入生产,没有持续不断减低生产批量的概念。
5、物料大批量地在工位间流动。但是整体流程方面缺乏流动的概念,导致了过度生产;对在制品库存的储存场地组织仍然是推动式的生产方式。
从整体情况看,现场管理体系还不够精细化,没有有效的持续改善体系在起作用,没有全员的持续改善的观念和系统支持。生产运作效率体系方面做的不够。人员状态不够积极,没有迹象显示充分参与生产管理与改善。整个制造体系还有很多改善的余地。
作者:博革咨询